Non-Ferrous Alloys & Strengthening
- Engineering
- Nov 25, 2020
- 5 min read
Updated: May 12, 2021
In this notes sheet...
Alloys are metals mixed with other materials.These could be metal or non-metal. They are commonly used instead of pure metals, as pure metals generally have low strength and high ductility – generally in engineering, we want the opposite.
There are a number of key definitions:
A component is one of the elements mixed in the alloy
A phase is a region within a material with uniform chemical and physical properties
The solvent is the main component of the allow: the element/compound in highest concentration
The solutes are the elements/compounds that are mixed in with the solvent: they are in lower concentration
A solid solution is a homogeneous single-phase mixture of solute in solvent
The composition of a component is the percentage mass of that component in an alloy or phase
The constitution is the overall sum of phases
Types of Alloying
There are a number of different types of alloys, with different methods used to make them.
Substitution

This is when solute atoms replace some solvent atoms.
For this to work, the Hume-Rothery rules must apply. According to these, the solute and solvent atoms should:
be similar in size (diameters within ~15%)
have the same general crystal structure
have the same number of valence electrons
have similar electronegativity
If these rules do not apply, there will be too much lattice distortion and an alternative crystal structure will form.
Interstitial Addition
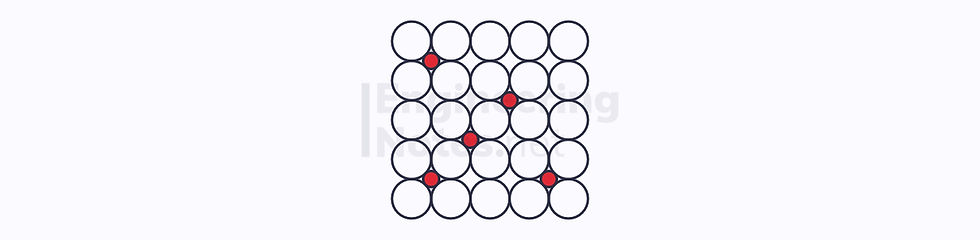
This is when smaller solute atoms fit between larger solvent atoms.
In order for this to occur, the diameter of the solute atoms must be smaller than about 0.6 the diameter of the solvent atoms.
Generally, the elements that are small enough to fit in the interstitial sites of solvent structures are:
Boron, B
Carbon, C
Chlorine, Cl
Hydrogen, H
Nitrogen, N
Oxygen, O
Phosphorus, P
Sulphur, S
When all the interstitial spaces are filled, the alloy is said to have reached its limit of solubility.
Solid Solutions

This is when solvent and solute atoms mix to form a single, homogenous structure.
Complete solid solubility occurs when two metals with similar atomic diameter are melted together. As they cool slowly, the solute atoms diffuse throughout the solvent creating a uniform single phase.

Some compounds mixtures exhibit partial (limited) solid solubility. This means that they can only form a single phase up to a certain composition. Beyond this, no solute can dissolve in the solvent, and so settles in a separate phase.
Sugar in water is a common example: initially, all the sugar dissolves. Keep adding more, however, and it will settle on the bottom – the limit of solubility has been reached.
Complete Solid Solutions
Equilibrium phase diagrams represent the different phases present at different compositions of alloys. They are different for complete solid solutions and ferrous and non-ferrous partial solid solutions.
The cooling process that forms solid solutions is, obviously, a function of temperature. We can plot this with respect to time for different compositions of the alloy on cooling curves:

For pure substances, there is no change in temperature as the change in state occurs. In the solidification process (freezing), this is due to the latent heat of fusion: during phase-change, there is no change in kinetic energy in the particles, only the potential energy changes.

However, for a solid solution the solidification process occurs over a range of temperatures. Between these two temperatures, there is a two-phase region where some of the compound with the higher melting point starts to precipitate in the still-liquid compound with the lower melting point.
The extent of this two-phase region depends on the composition of the alloy, and is shown on an equilibrium phase diagram:
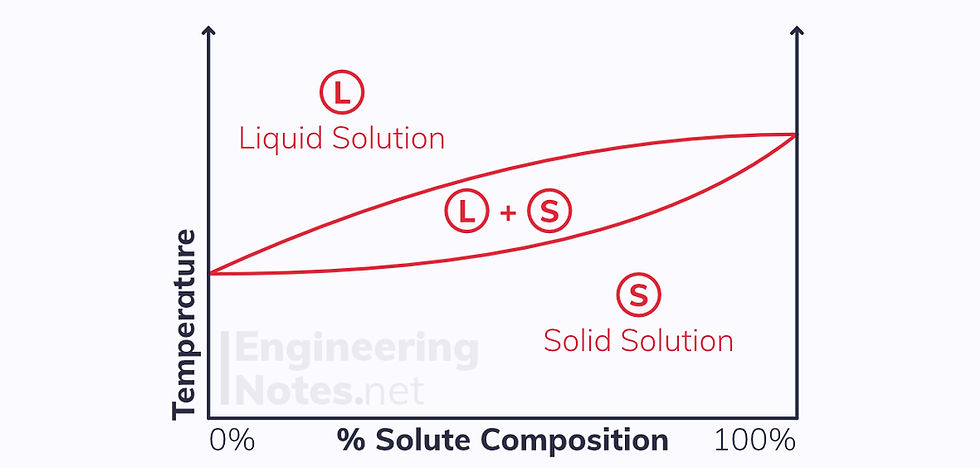
Linear Interpolation (Lever Rule)
Linear interpolation can be used to find the ratio of liquid to solid in the two-phase region, at a given composition and temperature:
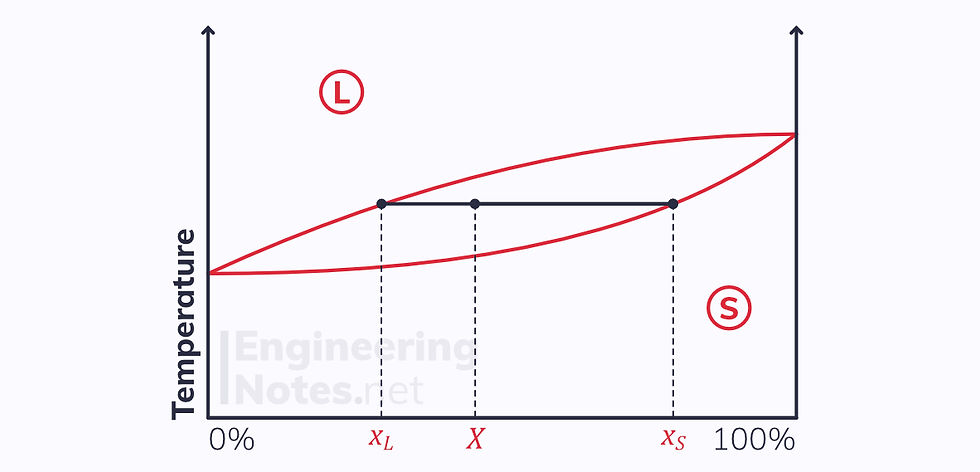
When in the two-phase region, the total mass of the substance is given as the sum of the masses of the liquid and solid phases:

The mass of liquid phase is given as:

The mass of solid phase is given as:

Sometimes, this is called the ‘Lever Rule’
Partial Solid Solutions
Pure substance are not mixed, and as such there is no difference in complete and partial solubility cooling diagrams when there is no mixture:

However, when two components are mix as a partial solid solution, the change of state occurs at a lower temperature range:
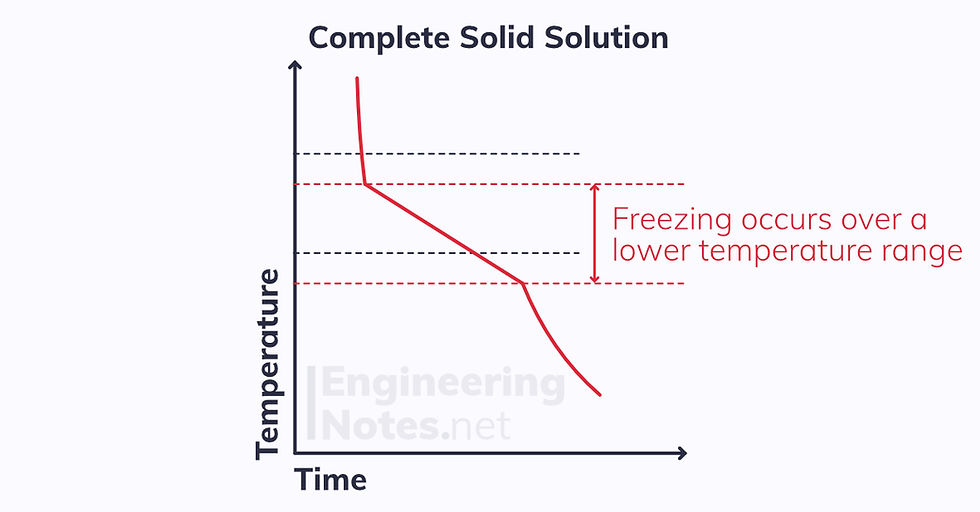
This leads to a drastically different equilibrium phase diagram (this example is tin, Sn in lead, Pb):
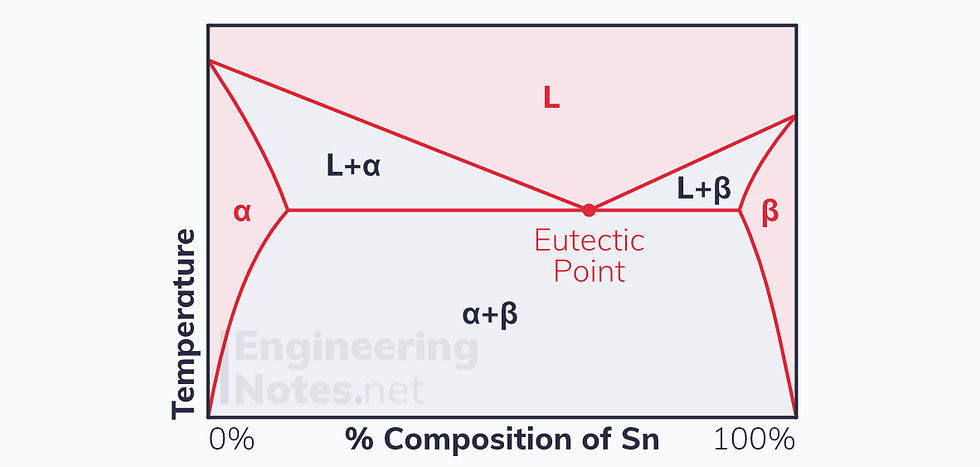
There are three single-phase regions, shaded red:
α phase: solid solution of Sn in Pb
β phase: solid solution of Pb in Sn
L phase: liquid solution of Pb & Sn
There are also three two-phase regions, shaded grey:
L+α Phase: liquid solution of Pb & Sn with some solid Pb in it
L+β Phase: liquid solution of Pb & Sn with some solid Sn in it
α+β Phase: mixture of non-uniform Pb & Sn
The eutectic point is the composition and temperature at which the liquid solution is in equilibrium with multiple solid phases.
Eutectic Microstructures
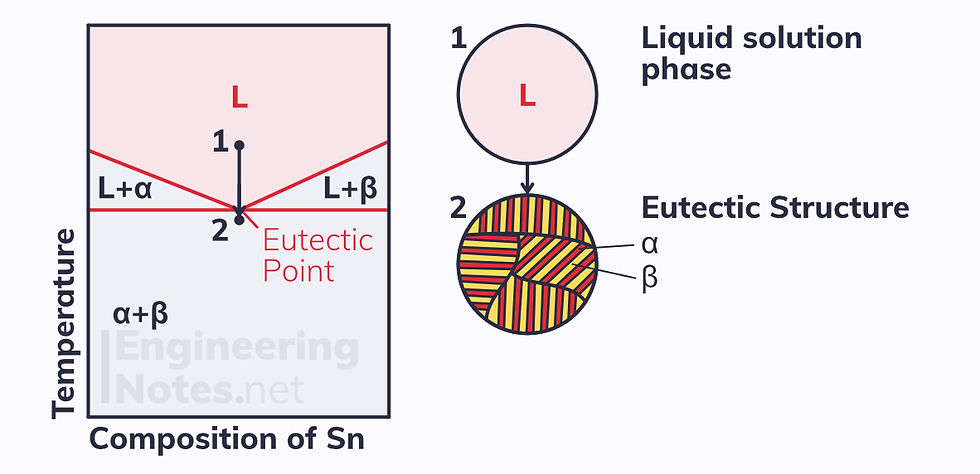
As you can see, if you cool a non-ferrous partial solid solution alloy at the eutectic composition, you pass through two distinct microstructures.
The eutectic structure is a lamellar form of uniform layers of α and β. The isotherm (horizontal constant temperature line) on which this lies is the eutectic line:
At the eutectic point, the structure is 100% eutectic
As you go away from the eutectic point, the percentage of the structure that is eutectic decreases
At either end of the eutectic line, the structure is 0% eutectic
The same linear interpolation as seen above for complete solid solutions can be used to find the amount of eutectic structure present at a given composition.
Low-Solute Composition Microstructures

When slow cooling at low solute compositions, four microstructural stages are passed through.
Again, at each stage, the proportional microstructures can be calculated using interpolation.
Solid Solution Hardening
In a completely solid solution, there is only one phase, consisting of solvent and solute atoms. Generally, the solute atoms are slightly larger or smaller than the solvent atoms:

When the solute atoms are smaller than the solvent atoms, a tensile strain field is induced in the crystal lattice.
The solute atoms will migrate to a compressive strain field in the lattice, reducing the overall strain.
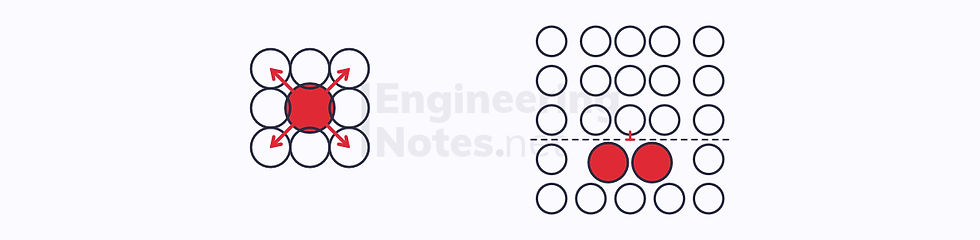
When the solute atoms are larger than the solvent atoms, a compressive strain field is induced in the crystal lattice.
The solute atoms will move to a tensile strain field in the lattice, reducing the overall strain.
When the solute atoms settle in the dislocation sites, they impede dislocation movement.
This means more energy is required to deform the material: it has been strengthened.
Precipitation Hardening
Unlike solid solution hardening, precipitation hardening introduces a second phase to the lattice. This second phase impedes dislocation movement, and the finer and more evenly distributed the second phase precipitates are, the better the hardening effect.
As the slow cooling equilibrium phase diagram above (Figure 5.13) shows, the β precipitates that form in stage 4 are coarse and concentrated along the α grain boundaries. This makes the alloy quite soft.
Precipitation hardening therefore consists of rapid cooling: it is a non-equilibrium process and leads to far finer β precipitates spread evenly throughout the α grains.
There are four steps involved:

Solution treatment – the alloy is heated to form a single-phase solid solution
Quenching – the alloy is cooled so quickly that no β precipitates can form: the solution is supersaturated
Heat treatment – the solid solution is heated to a specific temperature for a specific amount of time, allowing gradual diffusion to occur: fine β precipitates form throughout the α grains
Cooling – the two-phase alloy is cooled to room temperature without altering the microstructure
Precipitation hardening only works if the second phase gets more soluble as temperature increases.
Nucleation & Diffusion
Nucleation is the process by which the β precipitates form.
Diffusion is the process by which the newly formed β precipitates disperse throughout the α grains.
To achieve the evenly distributed, fine β grains throughout the structure, a balance between nucleation and diffusion is required:

The optimal temperature for the heat treatment is at peak rate of formation.
The rate of formation of the second phase, D, is modelled by an Arrhenius rate law:

D is the rate of formation
Q is the activation energy required
R is the universal gas constant, 8.31
T is the temperature in Kelvin
This can also be represented on a time-temperature-transformation (TTT) curve:

Comentarios