Ferrous Alloys & Strengthening
- Engineering
- Nov 24, 2020
- 5 min read
Updated: May 12, 2021
In this notes sheet...
Ferrous alloys are alloys whose primary component is iron: they are generally mixed with carbon, and split into two groups:
Steels have < 1.7% Carbon
Cast Irons have 1.7 - 4% Carbon
Each group is further split into subgroups:
Steels
Low Alloys
≤ 0.3% C These are low carbon, high strength steels used predominantly in construction
0.3 – 0.7% C These are medium carbon, heat treatable and so can be made very hard – used for railway tracks
0.7 – 1.7% C These are high-carbon, high-hardness steels, used for cutting tools
High Alloys
These are steels mixed with more atoms to form complex alloys
Stainless steel is an example: 18% chromium and 8% nickel
Cast Irons
1.7 -4% Greater than 4% C, cast iron becomes far too brittle for practical use
There are many versions of cast irons: white iron only consists of iron and carbon, grey iron may include silicon, magnesium, cerium etc.
Pure Iron
To understand the microstructures and mechanical properties of ferrous alloys, we need to understand pure iron (iron with less than 0.03% C by weight).
There are three forms of pure iron:
Ferrite, α-Fe: This occurs at low temperatures, below 910°C, has a BCC structure and is magnetic
Austenite, γ-Fe: This occurs at medium temperatures, between 910 & 1391°C, has an FCC structure, and is not magnetic
δ-Fe: This occurs at high temperatures, above 1391°C. It has a BCC structure
Fe-C Alloys
These three different forms of pure iron give rise to different alloyed forms depending on temperature. For this reason, the equilibrium phase diagram for Fe-C alloys is slightly different to those of non-ferrous alloys (there is an additional layer).
The interstitial solid solutions of C in Fe on the equilibrium phase diagram are also called α, γ, δ because the crystal structures are retained. These are not pure iron, however, but are Fe-C alloys.
δ -Fe does is not generally of interest.
Cementite, Fe₃C
Cementite is a hard, brittle compound that forms in addition to the ferrite and austenite phases in Fe-C alloys. It has a fixed carbon content of 6.7% C.
Equilibrium (Slow) Cooling

Single phase regions are labelled in red, two-phase regions in grey
Because of the second layer in the equilibrium phase diagram, there is a eutectoid point as well as a eutectic point.
At the eutectoid point, three solid phases are in equilibrium (α, γ & Fe₃C)
At the eutectic point, a liquid is in equilibrium with two solid phases (γ & Fe₃C)
The eutectoid point lies at 0.76% C at a temperature of 723°C
The eutectic point lies at 4.3% C at a temperature of 1130°C
Eutectoid Structure
When austenite is slow-cooled at the eutectoid composition (0.76% C), the single solid phase turns into a two-phase lamellar ferrite-cementite structure at the eutectoid point, 723°C. When it is further cooled, the eutectoid structure remains unchanged.

The eutectoid structure consists of laminated sheets of cementite in ferrite.
At 723°C, the structure is zero % eutectoid at 0.22% C and 6.7%C, but 100% eutectoid at 0.76% C. Interpolation (the lever rule) can be used to find the ratio of eutectoid to non-eutectoid microstructure along this isotherm, or any isotherm below 723°C.
Hypo-eutectoid Structure
Hypo-eutectoid refers to compositions below the eutectoid composition (0.76% C). When austenite is slow cooled at below 0.76% C, the α+γ phase is passed through, and the end result is not purely eutectoid.

The end result, point 4, is a two-phase equilibrium structure of pro-eutectoid ferrite (α) along the former austenite (γ) grain boundaries and pearlite in between – a lamellar structure of eutectoid ferrite and cementite.
Pearlite is what makes the alloy hard: cementite is an extremely hard (but brittle) compound, and the fine lamellas obstruct dislocation movement, giving the material an increased resistance to wear and indentation (hardness).
Hyper-eutectoid Structure
As you might expect, hyper-eutectoid refers to compositions above the eutectoid point. When austenite is slow cooled, it passes through the γ +Fe₃C region before passing the eutectoid temperature (723°C).

The end result is a two-phase equilibrium structure of cementite (Fe₃C) along the former austenite (γ) grain boundaries and pearlite in between – a lamellar structure of ferrite (α) and cementite.
Cast Irons
Cast irons all have between 1.7 and 4%C, giving them a hyper-eutectoid structure.
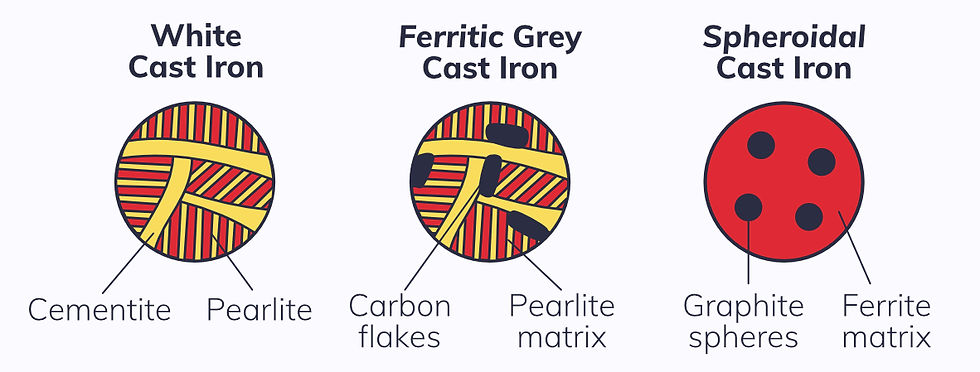
White cast iron has only carbon as a solute, and this is found throughout the structure as cementite and in pearlite.
Adding 2% silicon, magnesium, and cerium as well as carbon as solutes creates different microstructures:
Ferritic grey cast iron: graphite flakes suspended within a ferrite matrix lead to a high number of stress concentrations, making the material very brittle.
Spheroidal cast iron: graphite spheres suspended within a ferrite matrix reduce stress concentrations, making the material stronger and less susceptible to fracture.
Heat Treatment
Heat treatments are used to make carbon steels with superior mechanical properties to simple slow-cooled steels or cast iron.
Normalising
The pearlite that forms in equilibrium cooling (as described above) is very coarse, because of the very slow cooling process (annealing).
Using faster air-cooling leads to much finer pearlite, with a far denser lamellar structure. This is because the atoms do not have time to diffuse over a long distance and is known as normalising.

Fine pearlite is much stronger, because there are far more, tightly packed grain boundaries. These are very good at impeding dislocations, however this increase in strength comes at the expense of ductility.
Moderate Quenching
Quenching is the process of rapid cooling. If the transformation of austenite (γ) occurs fairly quickly, bainite forms instead of pearlite. The two are very similar, but bainite forms as very small needles of cementite in a ferrite matrix, rather than regular laminated layers of each:
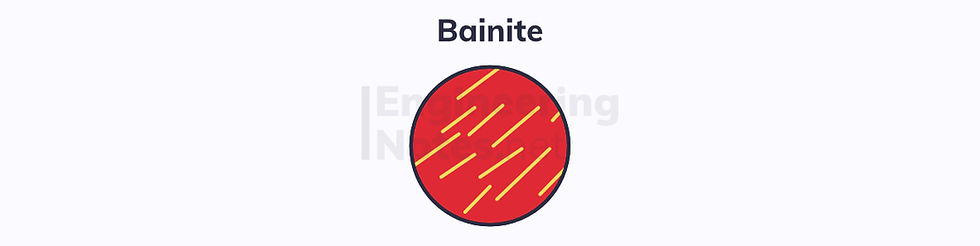
Bainite forms at lower temperatures than pearlite – around 250-500°C, as opposed to ~700°C
Rapid Quenching
If the austenite (γ) is cooled very rapidly (faster than 100°C/s), there is no time for any diffusion of atoms to occur, and so the austenite does not transform into ferrite. Below ~550°C, austenite is so unstable that it deforms via displacement (not diffusion) into a body-centred tetragonal arrangement (BCT).
This is a single-phase structure known as martensite – a supersaturated solution of C in Fe. It is very strong and hard, but incredibly brittle.
Martensite only forms below 0.7% C
This is because the temperature at which it forms decreases as carbon content increases, and at greater than 0.7% C, the temperature is below room temperature.
Generally, not all the austenite will transform into martensite. This leads to a two-phase structure of thin martensite needles surrounded by lighter γ:
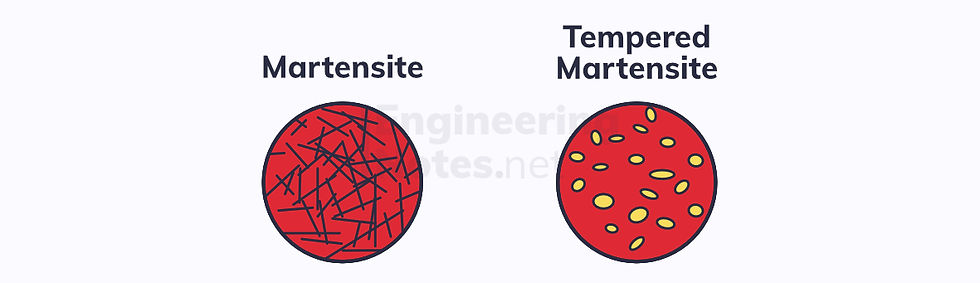
Martensite left as it is far too brittle for most engineering uses. Therefore, it needs to be tempered to restore some ductility. This is done by heating it to 250-300°C or 500-650°C and holding it there for a certain amount of time, allowing controlled diffusion to occur.
Tempered martensite consists of small, smooth cementite phases within a ferrite matrix.
The size and smoothness of these particles depends on the temperature and duration of tempering:
If the particles are too small, too large, or too smooth, they are ineffective at impeding dislocation movement
If the particles are not smooth enough, they cause stress concentrations that can lead to fracture
TTT Diagram of Heat Treatments

This diagram is for steel at the eutectoid composition. Note that the martensite is at around zero degrees at this composition, which is not practical – this graph is for demonstration only, and you would not find martensite at this composition in the real world.
Comments