Ceramics
- Engineering
- Nov 22, 2020
- 2 min read
Updated: May 12, 2021
In this notes sheet...
Ceramics are inorganic, non-metal compounds with very lough toughness but incredibly high hardness and low temperature and corrosion resistance.
There are basic ceramics that have been used for thousands of years (for bricks, vases etc.), and today there are complex high-performance ceramics with very specific applications.
Crystal Structure
Ceramics exhibit both ionic and covalent bonding between ions, and the extent of this is described by the degree of ionic character: MgO is 73% ionic, whereas SiC is only 12% ionic.
The crystal structure of a ceramic is typically far more complex than that of metals, as there are multiple cations (positive ions) and anions (negative ions). Most ceramics have a highly organised structure, but glass is an exception: it is not crystalline:
Glass is amorphous.
Properties of Ceramics

The stress-strain properties of ceramics are not investigated using a typical tensile test, as they are hard to grip:
Grip too hard, and they fracture
Don’t grip hard enough, and they move out of alignment
Instead, a bending test is performed:

Fracture occurs at the lower side, as this is in tension.
Ceramics are better in compression than in tension.
Steels, on the other hand, are better in tension. This is why reinforced concrete is such an excellent construction material.
Young’s Modulus
Very high, as the ionic bonds are stiffer than metallic bonds.
Strength
Very high strength, as the ionic bonds require significantly more energy to be broken than metallic bonds.
Ceramics very rarely break due to tensile yielding, however, as they are likely to fracture before reaching their UTS
Ductility
Not ductile at all: slip is very difficult in ionic structures, as like-charged ions would need to pass each other. Overcoming these repulsive forces would require an extremely high shear stress.
Toughness
Generally pretty low toughness, due to the many internal defects that form in the manufacturing process. These stress concentrations lead to brittle fracture.
Hardness
Very high hardness, so ceramics are often used as abrasives or cutting surfaces.
Creep Resistance
Good – ceramics only creep at temperatures significantly higher than metals.
Fatigue Resistance
Generally alright – fatigue requires a crack to initiate and propagate, but the reduced slipping capacity from the ionic bonding makes propagation difficult. Generally, a crack will either break the ceramic right away or not at all.
Density
Lighter than most metals – around 2.5 to 6 Mg/m³
Conductivity
Excellent thermal and electrical insulators – ionic and covalent bonding has no free electrons.
Corrosion Resistance
Excellent, as ceramics have already undergone corrosion.
Melting Point
Very high, due to high bond energies: between 1,900 and 2,800°C.
Manufacturing Ceramics
The melting point of ceramics is far too high to melt them and pour them into a mould: what do you even make the mould out of!?
Pressing
Instead, ceramic particles are mixed with a bonding agent (typically water) and pressed into shape:
Uniaxial powder pressing applies a force in one direction only and is the most common form. It leaves many irregularities in microstructure and density.
Isotactic powder pressing applies a uniform force from all directions, creating a far more uniform structure and density. However, it is more complex and expensive.
Sintering
After pressing, ceramics are sintered (heated to allow them to set/cure). This causes the grain boundaries between neighbouring particles to coalesce:
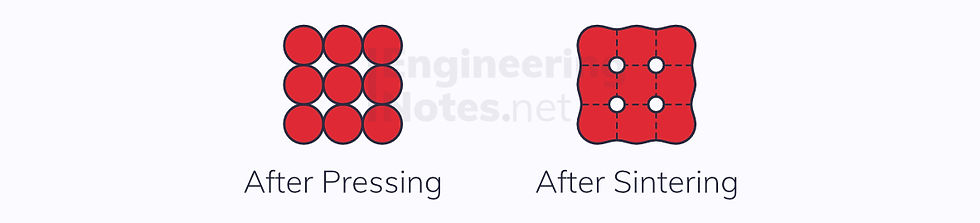
This leaves spherical voids/pores in the structure – these are what cause the low toughness in ceramics.
Comments