Polymers
- Engineering
- Nov 21, 2020
- 5 min read
Updated: May 12, 2021
In this notes sheet...
Broadly, polymers (also known as plastics) are split into three types:
Thermoplastics
Thermosets
Elastomers
Each type has a specific set of properties that are dictated by its structure and the bonding within the polymer.
Polymeric Structure
All polymers consist of long macromolecules which contain chains of covalently bonded atoms. The process of turning single monomer molecules into long chains of polymers is known as polymerisation:

Polymerisation is a chemical reaction that generally happens at high temperatures with the help of a catalyst (this is to break the double bond between the carbon atoms).
The schematic above shows the polymerisation of ethylene, C₂H₄ into polyethylene (PE).
Chains are typically between 10³ and 10⁵ monomers long.
The molecular weight of the polymer is the product of the chain length and monomer weight.
Chains vary hugely in weight, and so commercial polymers are classified in terms of mean molecular weight:

The chains can be linear, branched, or cross-linked networks:

This is what dictates their properties.
Bonding
Monomers are bonded as chains with covalent bonds
Chains are connected at branches and cross-links with Van der Waals bonds
Often, hydrogen bonds form here too
Thermoplastics
As seen above, these can be regular semi-crystalline structures or amorphous (no ordered structure). The more branches there are to a chain, the less regular the structure.
We say semi-crystalline, as no polymers are truly ordered. All thermoplastics contain crystalline and amorphous regions.
The Van der Waals bonds between chains break when heated at lower temperatures than the covalent bonds holding the monomers as chains. This means they easily melt and can be formed into different shapes over and over again.
Semi-Crystalline Thermoplastics
Some of the most common examples include:
Polythene (PE)

Very cheap
Easy to mould
Tough
Generally used in bottles, packaging, pipes
Polypropylene (PP)

Same properties as PE, but stiffer
Good UV resistance
Fatigue resistance
Used as fibres, outdoor furniture, rope
Polytetrafluoroethylene (PTFE)

Excellent temperature and chemical resistance
Good non-stick properties
Used in lubricants, chemical containers & bottles, non-stick surfaces
Amorphous Thermoplastics
Common examples are:
Polystyrene (PS)

Transparent
Very cheap
Very mouldable
Brittle
Can be expanded into foam
Used for stationary, packaging, food containers, electrical insulation
Polyvinylchloride (PVC)

Cheap
Stiff but brittle
Can be expanded into foam
Used in window frames, sheeting, artificial leather, fibres
Polymethylmethacrylate (PMMA)

Transparent
Water resistant
Used for windows, laminates, surgical instruments
Thermosets

Thermosets are highly crosslinked and amorphous. They are generally formed by mixing two compounds which undergo a chemical reaction.
This reaction is irreversible, forming strong crosslinks between chains. Therefore, they do not soften or melt when heated, and cannot be reformed.
Uses for thermosets are specialist:
Epoxies are used as a matrix for fibres in composites and adhesives
Phenolics are used in motor housing, telephones, and electrical fixtures
Thermosetting polyesters are used for composites, helmets, and automotive bodies
Elastomers

Many double carbon bonds remain intact in elastomers, so there are few crosslinks between chains. This makes them extremely elastic.
The more cross links there are, the more brittle and less elastic the elastomer becomes. Elastomers do not soften or melt. They burn.
Examples of Elastomers
Natural Rubber (polyisoprene)

Harvested from the sap of the Hevea tree
Used in erasers and for latex
Synthetic Rubber (polybutadiene)

Synthesised via polymerisation
Used in car tyres
Neoprene (polychloroprene)

Used in oil resistant seals
Tensile Properties of Polymers

When a load is applied to a polymer:
Bonds may rotate
Chains may slip & disentangle
Chains may stretch
The slipping and disentanglement of chains is very easy in elastomers and thermoplastics, giving both very low stiffness and fairly low strength.
The crosslinks in thermosets, however, provide more stiffness, but at the cost of reduced toughness.
Tangent & Secant Modulus
Polymers rarely have linear sections on a stress-strain curve. As a result, the modulus cannot easily be measured as the gradient. Instead, there are two methods used:

Polymers & Temperature
The tensile properties of polymers are often hugely dependent on temperature. Take this graph of PMMA (amorphous thermoplastic), for example:
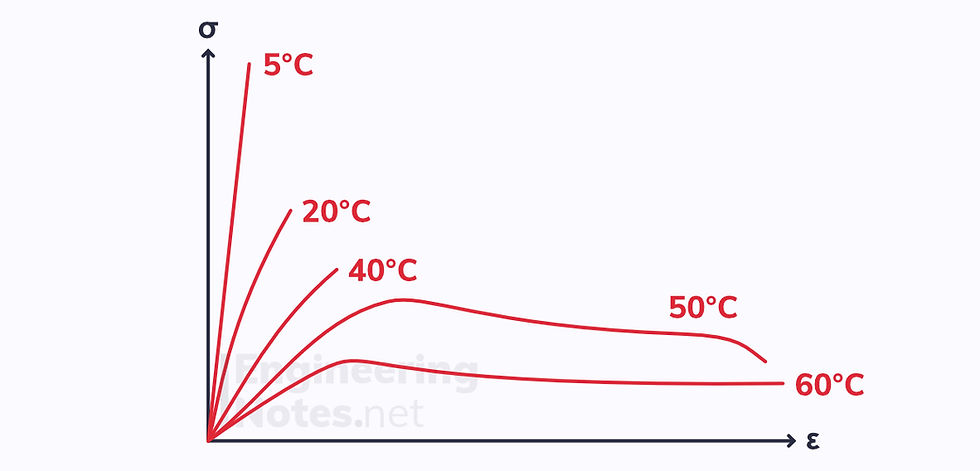
The change in properties occurs because as temperature increases, there is a change in specific volume:

At the glass transition temperature, secondary bonds between chains break apart allowing molecules to rotate (movement of side groups)
In an amorphous solid, there is free space in which the molecules can rotate, leading to a change in physical properties. Throughout the transition region, it is soft and rubbery.
Crystalline structures are incredibly dense, with little free space. The molecules have nowhere to rotate, so properties do not change in the transition region.
Semi-crystalline solids show a slight change.
Amorphous solids show a change in properties at glass transition, crystalline solids do not.
Temperature-Dependent Properties of Amorphous Plastics
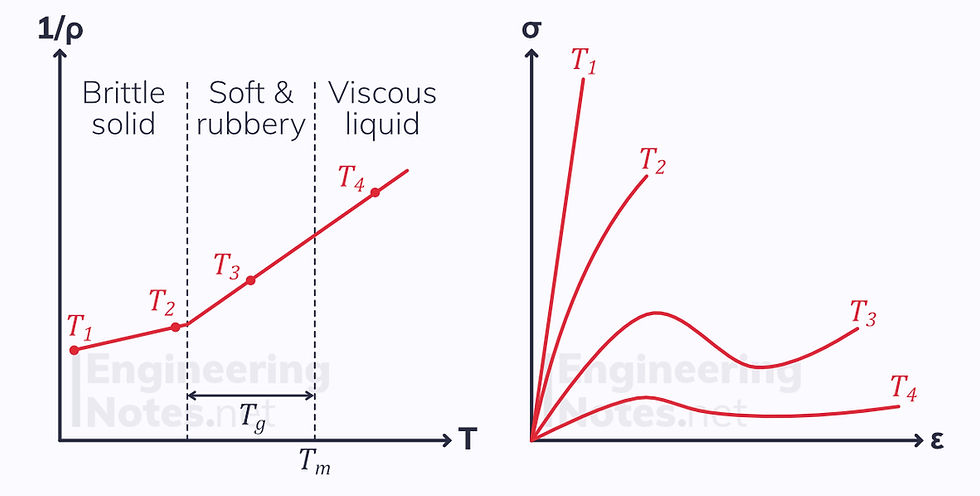
Modulus of Elasticity in Thermoplastics

Modulus of Elasticity in Thermosets & Elastomers

Both thermosets and elastomers are amorphous
They show a glass transition region, but do not melt
The more cross-links there are, the higher and more temperature-stable the elastic modulus
The process of adding crosslinks is called vulcanisation – this is done by adding sulphur
Creep in Polymers
Polymers are viscoelastic solids. This means their response to instantaneous stress is two-fold: there is an immediate strain followed by a time-dependent strain.

When an instantaneous load like this is applied to both an elastic and a viscoelastic solid, the strain responses vary:
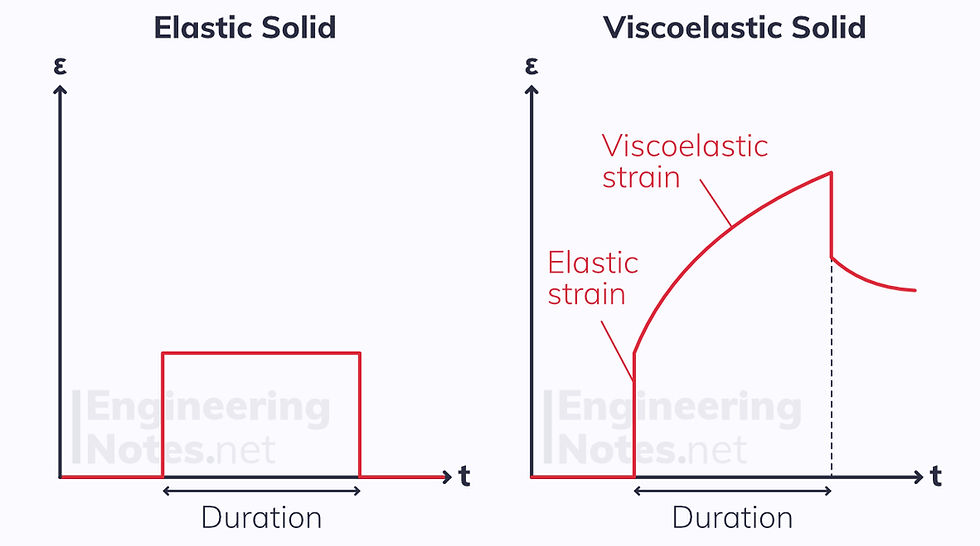
Creep in Polymers
Polymers creep at significantly lower temperatures than metals. In fact, polymeric creep is a serious issue even at room temperature, as the polymer chains uncoil so easily.
Creep is dependent on both temperature and applied stress:
The higher the temperature or stress, the faster the creep.
Unlike metals, there is no secondary steady-state creep region:

This strain response is defined by the polymeric creep law:

A and n are material constants
Creep Modulus
Since creep is dependent on stress, we can define a creep modulus as the constant applied stress divided by the strain with respect to time:

The lower the creep modulus, the easier the polymer creeps.
Failure in Polymers
Tensile Failure
The tensile failure mechanism in a polymer depends on its temperature – specifically, its temperature in relation to the glass transition temperature, Tg:
Below 0.75 Tg (in Kelvin), polymers are in the brittle, glassy region so fail by brittle fracture
This is likely to initiate at a surface defect, like a scratch of machining line
Above (Tg - 50 K), thermoplastics become plastic:
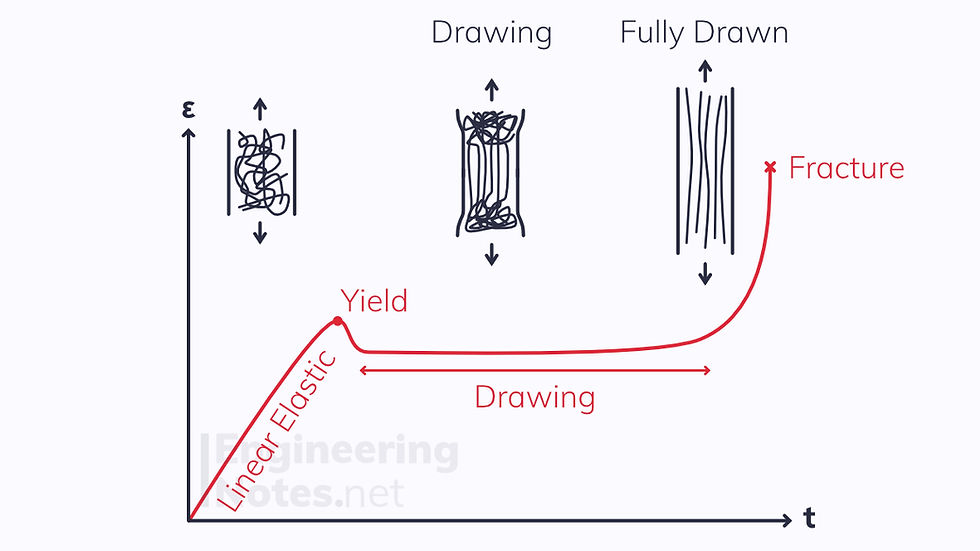
Initially, the thermoplastic deforms linearly elastically
Next, the thermoplastic yields
The thermoplastic is drawn out until all the chains are uncoiled
This massively increases the fracture strength, as at high stresses the chains are so spread out that they act as reinforcement fibres.
Plastics that do not draw at room temperature (e.g., polystyrene) undergo crazing:
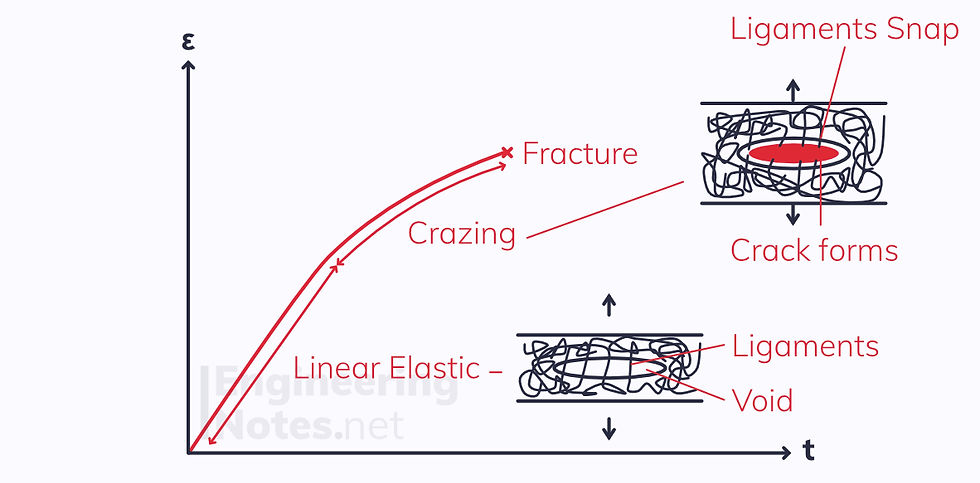
A microvoid in the polymer is held together with ligaments across the surface
Beyond the linear elastic region, these ligaments are drawn out
Eventually, the ligaments snap, and the craze becomes a crack
Crazing is what makes plastics appear white when bent: this is known as stress whitening.
Impact Failure
The energy required to break a polymer varies hugely with temperature, and is investigated using a Charpy impact test:
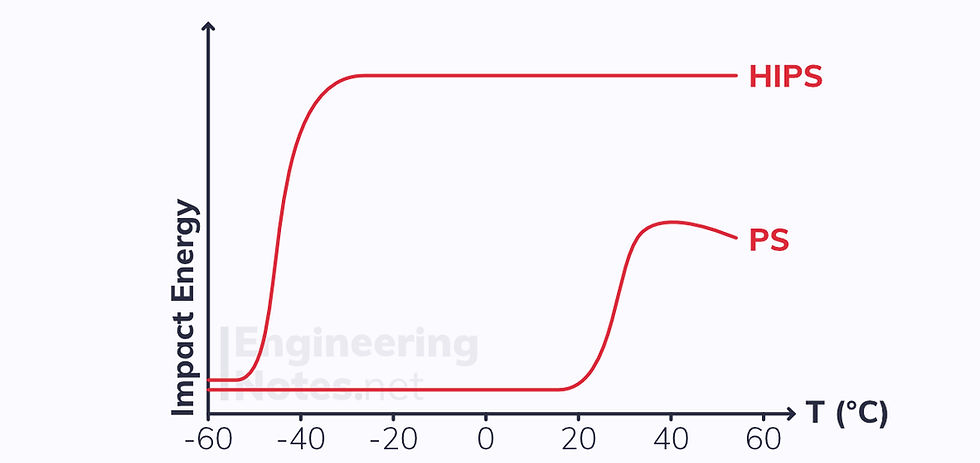
Note that modifying brittle polymers like polystyrene (PS) massively increases the energy required to break at standard temperatures: the modified plastic is called high-impact polystyrene (HIPS).
Fatigue Failure

Different polymers have vastly different fatigue behaviours. Some have fatigue limits, others do not:
Comments